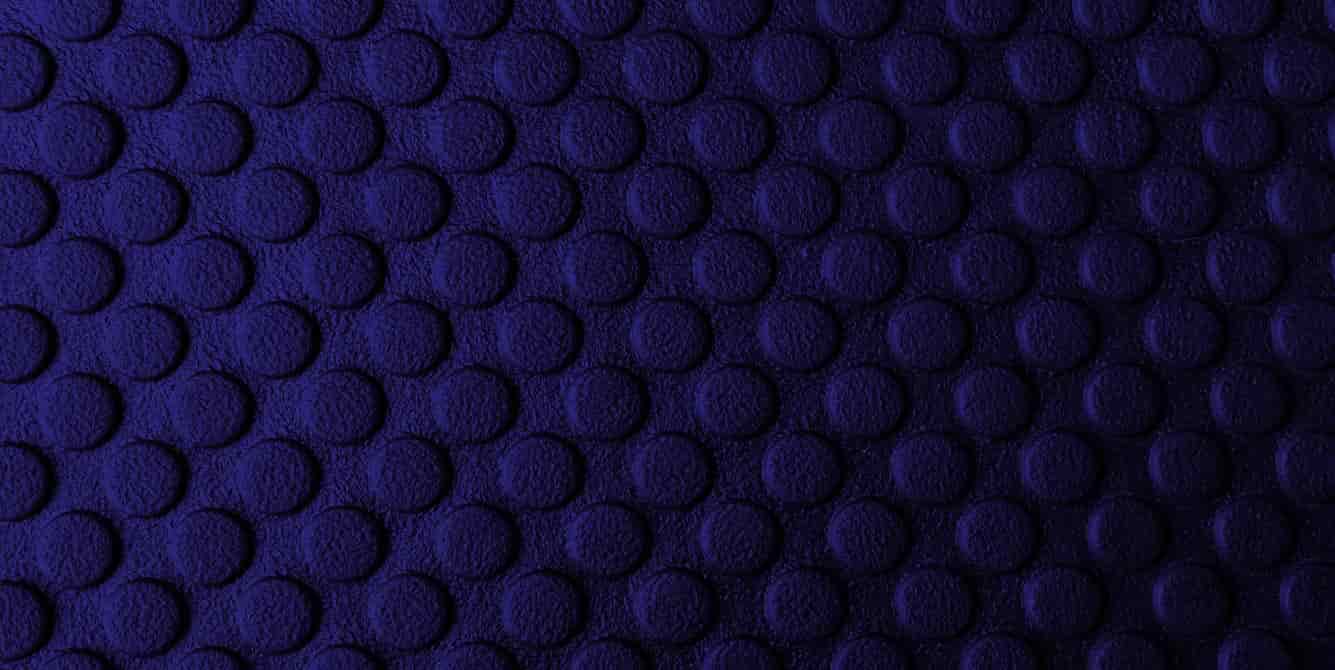
Factors Affecting Tolerances in Molded Rubber Parts
The tolerances of molded rubber products can be affected in a number of ways during the manufacturing process. Some of these factors are unique to the rubber industry and are listed below.
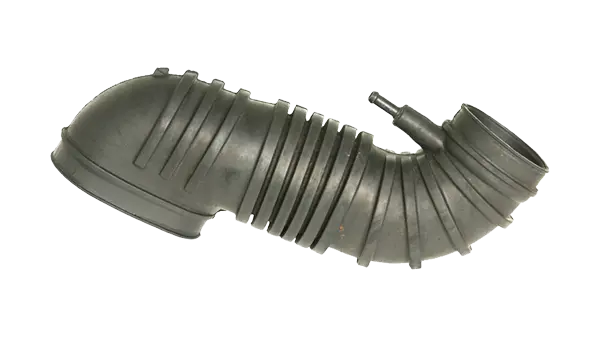
Mold Design
Molded rubber tooling can be built to varying degrees of precision, with more precise molds being more costly than those that are not as precise. Regardless of your precision requirements, our tooling will always attempt to yield the highest precision and longest mold life that the price of the mold will allow.
All molds will require some tolerances, however, and therefore some cavities will display variances from others. Thus, dimensional tolerances on the rubber product should allow for these slight variances. The accuracy of the mold register, or the various plates of the mold that come together to form the mold cavity, should also be considered.
A majority of molded rubber products will be made from two plate molds, while more complicated rubber parts will make use of molds with three or more plates. Some variation can be expected between plates and cavities in multi-cavity molds, which may cause mismatching or out-of-register manifestations in the part. These registering issues can usually be handled and controlled with sturdy dowel pins and bushings or by self registering cavities. In rubber products that require high precision dimensions and register, the machining and design work required in building the mold will be more precise, and thus the cost of these molds will be greater than those associated to commercial grade molds.
Inserts
Insert materials including metals, fabrics, plastics, etc. often have their own standards for tolerances. However, in designing molded rubber products that have inserts, other factors should be considered. These factors include:
- How the inserts fit in the mold cavities
- Proper hold spacing to match the inserts with mold pins
- Location of the inserts with respect to other dimensions
- The fact that inserts at room temperature must fit into a heated mold
Trim and Finish
Trimming and finishing operations work to remove excess rubber material that is not part of the finished product, such as flash. This process is often successfully completed without affecting important dimensions; in some instances, however, material can be removed from critical areas of the part itself. This can occur in tumbling, where the process may wear down the finished and exposed surface of the molded rubber parts. Mechanical trimming may be able to control dimensions in rubber parts with thin lips or projections in the mold parting line.
Distortion
Due to the flexible nature of rubber material, and the fact that it is affected by temperature, it is possible for distortion to occur when the rubber part is removed from the mold through the process of stretching it over a core. The rubber part can also experience slight distortion when it is packed to be shipped. Distortion can present difficulties in the measurements of rubber parts and should therefore be minimized through the practice of storing the rubber part in an unstressed state for 24 hours at room temperature after it has been molded.
Shrinkage
Shrinkage is the measurement of difference between two corresponding linear dimensions of both the rubber mold and the molded rubber part at room temperature. All rubber materials will display some level of shrinkage after the rubber part is molded and subsequently exposed to cooler temperatures. Shrinkage rates in individual compounds, however, will depend the rubber compound itself and will be affected by variables like cure time, rubber batch variance, temperature, post cure, pressure and the presence of inserts.
Mold design and compounding will include an estimation of the individual compounds shrinkage levels, which will then be incorporated into the mold design and cavity size. Even after shrinkage levels are incorporated into mold design, there still remains a level of variance that is unpredictable and therefore must be covered through dimensional tolerances.
Inserts in rubber products as well as complex molded rubber shapes can cause a limitation in lineal shrinkage in one direction while increasing it in another. Rubber shrinkage is a volume effect, and while it is our aim is to minimize the variables that contribute to shrinkage, they cannot be entirely eliminated.
Environmental Storage Conditions
Humidity — Some rubber materials will absorb moisture. Thus, depending on the material used in the molded rubber, some parts will exhibit changes in dimensions based on the amount of moisture present in the rubber product. In molded products that will exhibit these properties, tolerance for moisture expansion or contraction must be included in the dimensions. The effect of humidity on a rubber product can be minimized through stabilizing the product in an area where the humidity is controlled for a period no less than 24 hours.
Temperature — Changes in temperature will often cause changes in the dimensions of rubber materials. Different compounds will carry with them different coefficients of expansion based on environmental exposure to temperature. In rubber products that require critical or precise dimensions, the temperatures at which the rubber parts will be used should be measured and the time required to stabilize the part at said temperature should also be specified.
Dimension Terminology
Fixed Dimensions — Are parallel to the mold parting line or the parting lines of major mold sections and are those dimensions that are not affected by flash thickness variation.
- Example - A Sample wheel, with half of the wheel formed in each half of the mold and the flash line located around the O.D.
- The fixed dimensions are the OD and the hub diameter
Closure Dimensions — Are vertical to the mold parting line or to the parting lines of the major mold sections and are those dimensions that are affected by flash thickness variation.
Closure dimensions will be affected by a number of factors additional to those listed above including, weight and shape of raw material stock, flow characteristics of that stock, and types of flash grooves or other relief devices in the mold. These variables will all affect the final degree of mold closure.
Although affected by variations in flash thickness, closure dimensions are not always related to basic flash thickness. In manufacturing processes that include machine or die trimming a molded rubber product, the mold itself will be designed with a thicker artificial flash than rubber parts that are designed for hand deflashing or tumbling. Thus, although the same rubber part from two different sources may meet drawing dimensions, they may also exhibit a difference in basic flash thickness at the parting line depending on the molding process and deflashing method employed.
Most molded rubber parts will have a logical place for the mold designer to locate the parting line that allows for the soundest control of dimensions.