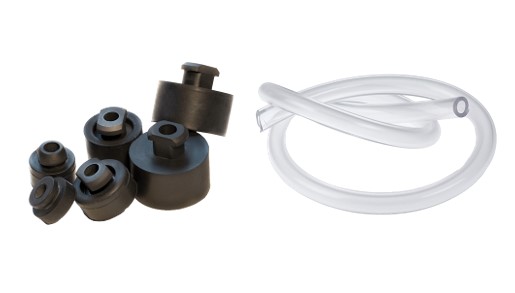
When it comes to manufacturing parts, material selection can make or break your investments. There are plenty of compounds to choose from, but some are better suited for your applications than others.
EPDM and PVC are two commonly used polymers for a variety of industries. Both compounds are go-to solutions for tubing, seals, and other parts, but one can be much better than the other depending on your performance needs and design requirements. It’s time to break down PVC vs EPDM to see which is better suited for your parts.
The Differences Between PVC and EPDM
While EPDM and PVC are seemingly quite different, both polymers share several characteristics. PVC, also called polyvinyl chloride, is a thermoplastic made by polymerizing vinyl chloride and introducing various additives to achieve certain properties. EPDM is a synthetic rubber known as Ethylene Propylene Diene Monomer and is made by polymerizing ethylene, propylene, and certain other alpha-olefin comonomers. In general, both materials boast excellent durability, weathering resistance, and ease of processing.
Of course, there are plenty of characteristics that these polymers don’t share. These performance requirements can be the difference between a good part and a bad investment for several reasons. The differences between EPDM and PVC include:
- Oil and solvent resistance
- Flame resistance
- Temperature range
- Hardness
- Color options
Material resistances
While both EPDM and PVC share some resistances, the latter can stand up to a few more substances. EPDM struggles in environments with oils, solvents, and other similar fluids. PVC doesn’t have this problem, making it more useful in certain medical, automotive, and other applications where your parts will need to endure these factors.
Flame resistance
Exposure to fire is another key criteria where one material performs better than the other. PVC has a much better track record in the hot seat as it’s very good at resisting flame. EPDM is naturally flammable, but can be made to be much more fire resistant with the addition of blockers and additives in the manufacturing process.
Temperature range
While EPDM is naturally less flame resistant, it does stand up to the heat better than standard PVC. EPDM can be used in temperatures as low as -60° F (-51⁰ C) and as hot as 350° F (177⁰ C). This synthetic rubber is also very stable at both high and low temperatures, making it a reliable general-purpose elastomer in a variety of conditions.
PVC doesn’t quite have the same temperature range as EPDM. This thermoplastic’s ideal range goes from -40° F (-40⁰ C) to 140°F (60°C). If that limited operating range is an issue, EPDM will give you a lot more temperature resistance in both hot and cold environments.
Color options
Performance isn’t the only factor that can make a difference. If you need your parts colored for installation, marketing, or some other purpose, PVC can easily be made to be black, clear, or some other color for both rigid and flexible parts. EPDM doesn’t share this quality. EPDM parts are typically going to be some form of black or gray, making it a less attractive option if you need clear or colored parts.
Invest in the PVC, EPDM, and Other Parts Your Business Needs
Whether you need roofing materials, automotive components, or any other plastic or rubber part, it’s best to invest in a long-term part solution. There are pros and cons to every polymer. It’s important to identify the best, most cost-effective material for your needs, whether it’s PVC, EPDM, or something else.
The good news is that you don’t need to find this solution on your own. Timco works directly with businesses to identify their part needs and supply them with a part solution designed around their application and budget. Ready to invest in quality parts custom-made to your exact needs? Give us a call at 800-969-6242 or contact us online to talk to one of our experts about your parts.