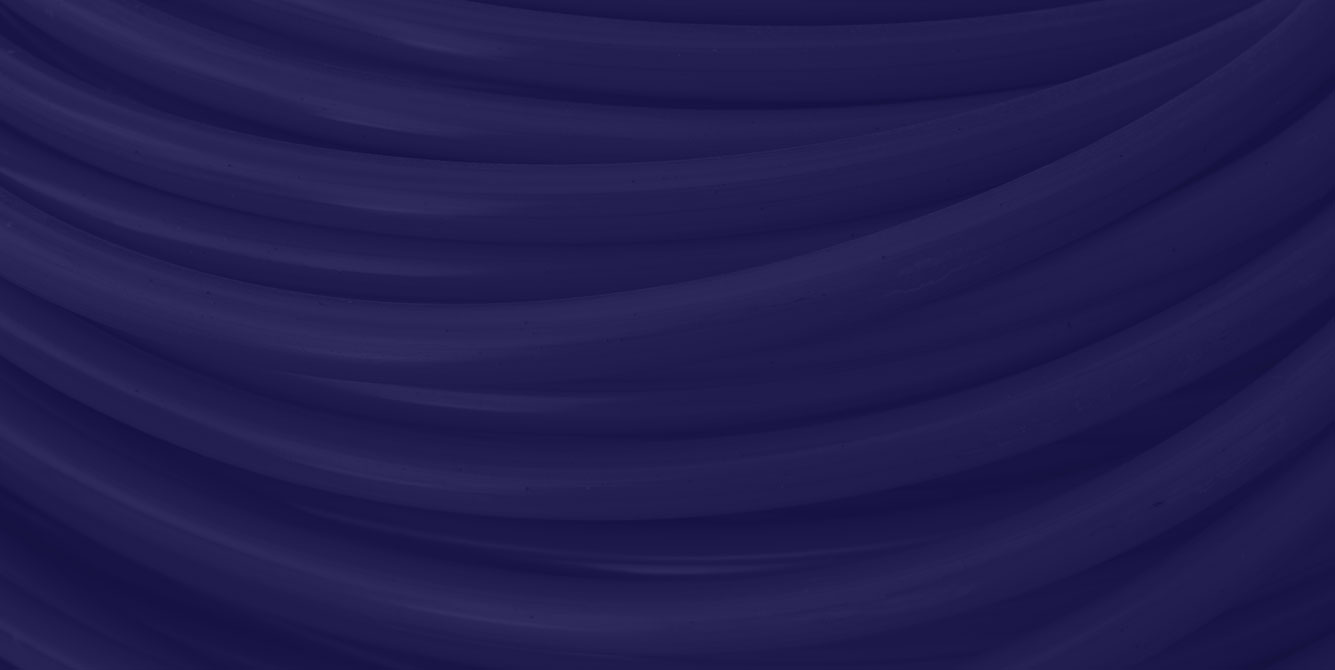
Silicone Rubber Material Manufacturer
Gaskets, Seals, Tubing & More
If you need a rubber product that can withstand difficult environments, silicone rubber can be an excellent choice for your applications. Timco Rubber works with businesses to provide custom-designed silicone tubing, o-rings, and other parts made specifically to address your application’s performance needs.
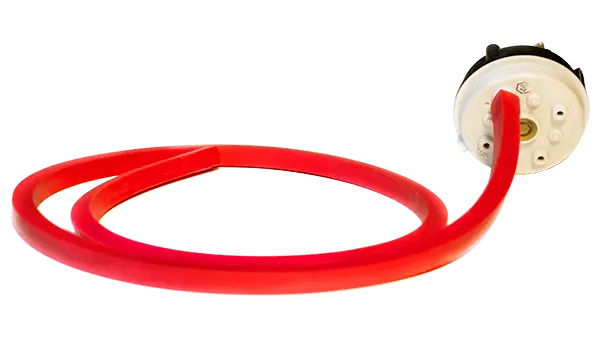
What is Silicone Rubber: A Material Made for Difficult Environments
Silicone is one of the materials of choice for any application that deals with environmental factors that can break down other solutions. When it comes to extreme temperature, silicone rubber offers a great range of resistance in both hot and cold environments. In addition, silicone provides far superior tensile strength, elongation, tear strength, and compression sets in extreme temperatures than conventional rubbers.
In addition to temperature resistance, other advantages of silicone rubber include insulation from electricity, compression set resistance, and the ability to repel water. These advantages make silicone rubber a versatile material that can help businesses invest in rubber products that not only withstand difficult conditions, but also perform as necessary for a long time. Because of these factors, Timco regularly provides businesses with silicone gaskets, tubing, and other custom parts.
What is Silicone Rubber Made Of?
As a synthetic rubber, silicone is not a naturally-occurring substance. It’s unclear who exactly invented silicone – some argue that the polymer was first discovered in the early 1800s by Swedish chemist Jöns Jacob Berzelius, while others credit English chemist Frederick S. Kipping with discovering silicone in 1840. Regardless, silicone rubber was popularized until the early 20th century when it quickly became an essential material in a wide variety of products.
There are several steps involved with making silicone rubber, starting with isolating silicone, a chemical element that must be isolated from silica. The first step is to heat quartz sands under extreme temperatures until it turns into pure silicone. That silicon is left to cool so that it can be turned into a fine powder and used to help produce everything from semiconductors to fire bricks.
In order to make the elastomer, silicone powder is heated along with methyl chloride and polymerized with oxygen and other elements to create polysiloxane. This raw version of silicone can be combined with coloring pigments and additives to add desired characteristics to the end material. Once ready, silicone rubber is then extruded, molded, or manufactured in some other way to be used as a final part.
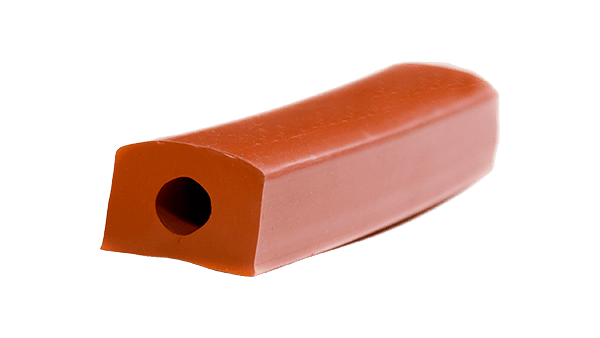
Silicone Properties
- Common Name: Silicone
- ASTM D-2000 Classification: FC, FE, GE
- Chemical Definition: Polysiloxane
- Temperature Range
- Low Temperature Usage: -60° to -150° F | -50°C to -100°C
- High Temperature Usage: Up to 480° F | Up to 250°C
- Tensile Strength
- Tensile Range: 200-1500 P.S.I.
- Elongation: 700% Maximum
- Durometer (Hardness) – Range: 30-90 Shore A
- Resistances
- Abrasion Resistance: Fair to Poor
- Tear Resistance: Poor
- Solvent Resistance: Poor
- Oil Resistance: Fair to Poor
- Aging Weather - Sunlight: Excellent
- General Characteristics
- Adhesion to Metals: Good
- Compression Set: Good
- Resilience/Rebound: Good
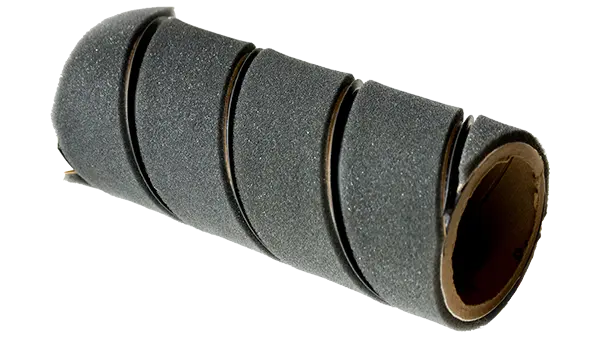
Silicone Applications
Automotive
- Sound and vibration dampening in automotive drive shafts
- Shaft sealing rings
- O-rings
- Window and door seals
HVAC
- Square, kink-free tubing
- High-temperature gaskets
- O-rings
Electrical
- Wire and cable jacketing
- Electrical safety stinger covers
- Conductive profiled silicone seals
Home appliances
- Rubber tubing
- Appliance seals
- O-rings
- Sound and vibration dampeners
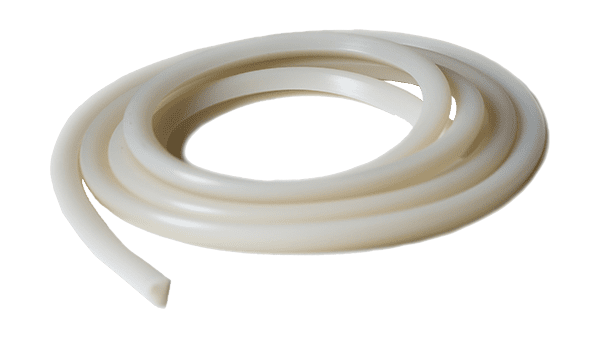
Silicone Benefits and Advantages
- Withstands high and low temperatures far better than organic rubber, with an operating temperature range from -150 to 480° F.
- Good thermal stability.
- Certain silicone compounds can withstand long-term, continuous use even at 200°C (392°F), while others may be able to withstand higher temperatures for short periods of use.
- Repels water and forms tight seals.
- Excellent electrical insulation, with no decline in insulation performance even when immersed in water
- Carbon black additives can further increase silicone's electrical conductivity.
- Flexible at low temperatures, stiffens up at higher temperatures.
- Under ordinary pressure, contact with steam typically causes little or no deterioration.
- Flame retardant with additives, with some products receiving UL94 V-0 certification according to the UL94 (USA) standards for flammability classification.
- Low chemical reactivity.
- Non-toxic and can be made to be FDA-approved for food contact.
- High levels of flexibility, both in terms of hardness and manufacturing production processes.
- Can be compounded in different ways to meet any number of applications (die cutting, injection molding, extrusion).
- Can be custom cut to length for various production part needs.
- Can be either clear or made with different colors.
- Fillers can improve tensile strength to roughly 1,500 PSA and tear resistance up to 200 lbs.
Timco: Your Go-To Custom Silicone Parts Supplier
Silicone is an excellent material for a variety of applications, but there are some instances where the compound is not a good fit. Polysiloxane does not hold up well when exposed to oil or solvents or if your part will face regular abrasion. There are also less expensive materials than silicone, so it’s essential to figure out which compound is best for your needs.
The good news is that you don’t need to figure out which materials are best for your applications by yourself. Timco partners with businesses to analyze your needs and determine a custom-designed part solution with the best, most-cost-effective material in mind. We partner with you to supply with tailored solutions and offer the following value-added services to help you save valuable time and money:
- Subassembly of rubber parts
- Kanban replenishment
- Kit assembly
- Flexible control methods
- Our in-house stocking program and on-time delivery
Want to make sure that Timco is the right partner for all your Silicone part requirements?
Silicone Rubber FAQs
Q: Is silicone rubber plastic or rubber?
Silicone is technically a synthetic rubber. While silicone can share some qualities with performance plastics like TPE and PVC, there are a few notable qualities that differentiate silicone and plastics, including high-end temperature resistance.
Q: What is the difference between silicone rubber and natural rubber?
Silicone is a synthetic rubber while natural rubber is made with rubber latex, a substance that can be harvested from plants. Natural rubber is mostly known as a tough material used for applications that must withstand extreme duress and regular wear and tear, while silicone excels in environments that require extreme temperature or weathering resistance.
Q: Is silicone rubber safe?
Silicone is non-toxic and regularly used for medical, electrical, and home appliance applications. Silicone can also be made to meet FDA regulations for food contact.
Q: Does silicone give off microplastics?
Unlike common plastics, silicone rubber does not shed microplastics thanks to its durable molecular structure.
Q: How durable is silicone rubber?
Silicone is a durable material that is excellent at withstanding extreme temperatures and regular exposure to the sun and other elements. However, silicone can be susceptible to more physically demanding applications, such as tearing and abrasion, although fillers can be added to improve silicone’s tensile strength and tear resistance.
Q: How long does silicone rubber last?
Silicone ages extremely well, even in demanding conditions. This material’s exceptional stability allows silicone parts to last for decades in ideal circumstances.
Interested in custom Silicone O-rings, tubing, and other parts?
Get a quote to find out more.
Not sure which material you need for your custom rubber product? View our rubber material selection guide.