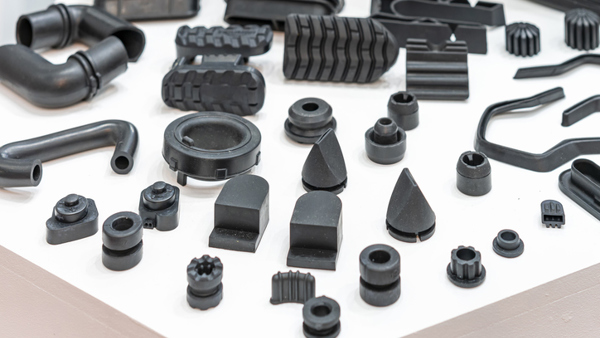
Choosing the right material for your parts isn’t a simple process. There are several different types of rubbers and plastic available, but some are better for your needs than others.
This process is even trickier when certain materials share characteristics. EPDM and natural rubber are two rubbers that provide a high level of physical durability, but there are other criteria that can make one a better fit for your parts. Let’s break down some of the main differences between EPDM and natural rubber.
Is EPDM Natural Rubber?
While EPDM and natural rubber share some similarities, they are not the same material. There are several differences between EPDM and natural rubber, starting with how they’re made.
As indicated by the name, natural rubber is made from a naturally occurring substance. Rubber latex has been harvested from plants since 1,600 B.C. and mixed with different ingredients to create different forms of natural rubber. EPDM rubber is a synthetic material that is made through the polymerization of ethylene, propylene, and certain other alpha-olefin comonomers.
The other main difference between EPDM and natural rubber involves how well they can hold up for various applications. Both materials are known for their physical durability, but certain environmental challenges and performance requirements can make one option better than the other. These different needs include:
- Weathering
- Heat resistance
- Tear resistance
- Adhesion to metal
- Compression set and resilience
Weathering
If your parts need to survive outside, EPDM is an excellent option. This synthetic rubber is ideal for any parts that need to withstand regular exposure to sunlight, ozone, and other outdoor elements. Natural rubber struggles with the same type of exposure, which can lead to premature part failure.
Heat resistance
EPDM is a better option is you need a higher temperature range. EPDM can operate up to 350 degrees Fahrenheit and provides excellent stability and steam resistance. Natural rubber caps at 175 degrees, a notable difference compared to EPDM.
Tear resistance
EPDM is an extremely durable material, but it can struggle with tearing over time. Natural rubber doesn’t have that problem. Parts made with natural rubber are extremely resistant to force that would tear other types of rubber, giving it an edge for parts like molded seals and hoses.
Adhesion to metal
Some materials adhere to metal better than others. EPDM is a solid option for rubber-to-metal bonded parts and can accommodate a lot of potential part needs. However, natural rubber truly excels when it comes to adhesion to metal, making it a great choice for particularly challenging rubber-to-metal bonded part designs.
Compression set and resilience
Compression set and resilience are other areas where EPDM is good, but natural rubber truly excels. Natural rubber is not only extremely resistant to deformation after being placed under pressure, but also rebounds back to its original shape better than most other compounds.
Uncover Whether EPDM, Natural Rubber, or Some Other Material is Right for You?
Choosing the right material can have a drastic impact on how well your parts perform. EPDM and natural rubber are both excellent options depending on your specific design needs and operating environment – the challenge is determining which material is right for your applications.
The good news is that you don’t have to go through this search alone. Timco works with businesses to provide a custom part solution tailored to their performance requirements and budget. Give us a call at 800-969-6242 or contact us online to talk to one of our experts about supplying parts customized for your applications.