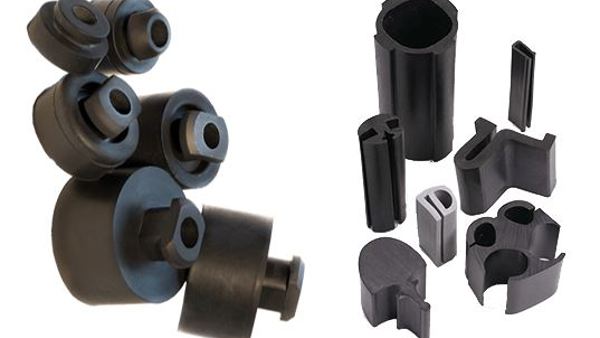
As pivotal components of many projects, rubber and plastic parts are critical to ensure successful design. However, certain compounds are better suited for some applications than other. It’s essential to identify which material is best suited for what your design needs.
Of course, this process can be complicated. With so many distinct types of rubber and plastic material accessible, it’s not always easy to choose which is right for your needs. For example, both EPDM and Neoprene are high quality materials, but can differ in what they specifically have to offer.
When it comes to Neoprene vs. EPDM rubber, it’s time to narrow down your project's performance requirements. Let’s break down which factors can help you determine which material is best for your parts.
The Differences Between Neoprene and EPDM
Both Neoprene and EPDM share certain benefits, but the compounds also boast special characteristics that may make or break the overall viability of your part. Those differences begin with how each material is made.
Neoprene is a synthetic rubber produced from chloroprene, a type of monomer found in petroleum. The polymerization process can vary, yielding either soft or hard Neoprene depending on its intended purpose and application method.
EPDM rubber is also knowns as ethylene propylene diene monomer. This compound was invented during experiments for a strong, flexible, and EPDM is now often preferred because of its durability and wide range of resistances.
A good way to approach making the right choice in the battle of EPDM rubber vs. Neoprene is to weigh a variety of factors. These factors include:
- Required material resistance properties
- Temperature requirements
- Physical durability and other characteristics
- Cost
Material Resistances
There are multiple environmental factors that can pose problems for specific materials. Both EPDM and Neoprene offer varying levels of resistance that will directly impact their viability for your application.
If you need a rubber compound that is made to survive in the outdoors, EPDM is typically a great option. EPDM offers excellent resistance to ozone and sunlight, allowing it to delay the gaining effects that would break down other materials. EPDM can also survive many chemicals and other substances, such as alkalis, oxygenated solvents, water, and steam. One major downside of EPDM is that it has poor resistance to oils and solvents, so it’s best to avoid EPDM if your parts will come in contact with these substances.
While not as resistant to aging as EPDM, Neoprene also boasts good resistance to sunlight and weathering. The biggest difference is that Neoprene enjoys good oil resistances and can operate in environments with solvents, making it a good choice to parts with intermittent exposure to these elements.
Temperature Requirements
Some compounds can withstand the heat and cold better than others. Both EPDM and Neoprene offer solid temperature resistance, although EPDM does offer an edge I this department.
EPDM provides excellent heat and steam resistance, with a temperature range of -60 degrees to 350 degrees Fahrenheit. Parts made with EPDM also enjoy high material stability or both the high and low end of the temperature range. Neoprene’s temperature range is a bit smaller at -50 to 250 degrees, although the material also boasts good flame-retardant and self-extinguishing characteristics.
Physical Durability
A material's durability and toughness is another critical factor in selecting the perfect rubber for a given application. The long-term viability of your parts can often come down to their physical capabilities, which is why EPDM and Neoprene make for attractive material options.
EPDM is one of the most durable man-made rubbers you can find. Between good abrasion resistance and compression set, EPDM offers a long-term part lifespan that allows for fewer replacement parts over time. In addition, EPDM is extremely versatile and can be custom molded, extruded, and otherwise manufactured in a variety of hardnesses.
Neoprene rubber is also extremely durable. This material is highly elastic and abrasion-resistant with outstanding tear resistance. Neoprene has an excellent balance between resilience, tear strength, and resistance to environmental conditions.
Cost
As a specialty material, Neoprene is the more expensive of the two compounds. Part of EPDM’s popularity is that it is very versatile and cost-effective. However, it’s important to weight performance needs before committing to a specific price. If your parts demand oil and solvent resistance, the cost savings of EPDM will quickly not matter. As such, balance both budget and performance needs into your decisions.
Invest in Quality EPDM and Neoprene Parts
Both EPDM and Neoprene are excellent options for rubber products, but it’s important to identify which is perfect for your design. Fortunately, Timco can help you decide which materials are best for their exact needs.
Timco partners with businesses to help them invest in customized part solutions. Our experts work directly with your team to identify specific performance requirements and supply the best, most cost-effective part solution for your application.
Ready to invest in the parts you need? Give us a call at 800-969-6242 or contact us online to talk to one of our experts or get a quote for your project.