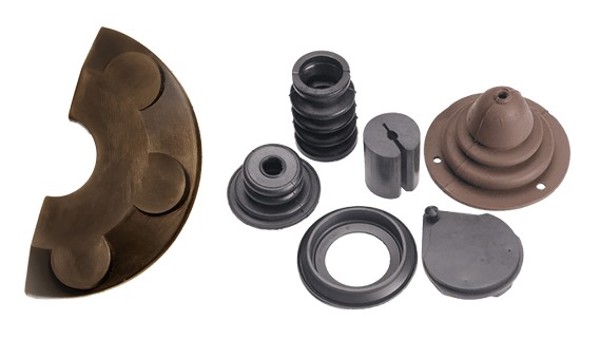
When you need rubber parts, there are plenty of options available to your business. The problem is that when you’re presented with so many different compounds, it’s hard to tell which one is better for your exact needs.
Viton and Nitrile are two different synthetic rubber materials that can help make or break the success of your parts. Each material is regularly used to make seals, gaskets, and other parts, but one can be a much better choice based on your performance requirements and budget. Ready to find out if Viton or Nitrile is right for your applications? Let’s break down each material to see why they might be right for your parts.
The Differences Between Nitrile and Viton
Both Nitrile and Viton are considered synthetic rubber, there are different processes to producing each compound. Nitrile, also known as Buna-N or NBR, is made when acrylonitrile (ACN) and butadiene are bonded through polymerization. The newly created material is then formed into sheet rubber and vulcanized with different ingredients to give the Nitrile various desirable performance qualities.
Viton (FKM) first came into notoriety when it was introduced to the aerospace industry in 1957. Originally marketed by DuPont, the Viton brand is now owned by Chemours and is manufactured with 100% pure fluoroelastomers. Since its introduction, Viton spread from aerospace applications to being used as a high-performance elastomer for applications that require premium performance.
Interestingly, Nitrile and Viton both share several characteristics and mainly differ in just how well they perform in certain environments or situations. Each material can be the difference maker between a good part and a bad investment for several reasons, so it’s important to identify which is best for you. Key considerations Viton and Nitrile include:
- Oil and other resistances
- Durability
- Temperature range
- Cost
Oil and other resistances
Arguably the most notable shared characteristic between the two materials is their resistance to oil and petroleum products. Still, there are specific instances where one part may be better in these types of environments.
Nitrile is a great option for parts that are constantly exposed to oil or operate in places where that oil is extremely concentrated. Viton takes that oil resistance and ticks it up a notch. This particular material is built for heavy duty applications that demand extreme chemical resistance, exposure to hydraulic fluids, and other extremely corrosive substances. For example, both Viton and Nitrile O-rings are built to succeed around oils and fuels, but Viton is the go-to option when you need extreme resistance.
Durability
Overall, both materials are quite durable. However, Viton is known for being about as tough of a synthetic rubber that you can find. Viton is designed to resist just about everything you can throw at it – there’s a reason it was originally marketed to the aerospace industry. Viton boasts good abrasion and tear resistance, is excellent at dealing with UV exposure, and can handle a wide range of demanding environments.
While Viton is exceptionally tough, Nitrile is no slouch when it comes to durability. Nitrile is not only great at resisting tears, abrasions, and other physical damage, but also offers excellent compression set resistance. The only major downside for durability is that it struggles with weathering and shouldn’t be used for outdoor applications.
Temperature range
Temperature range is another factor where both materials perform well. Once again, Viton has an edge when it comes to more demanding environments, especially when considering certain grades of fluorelastomers that can operate successfully in -40 degrees Fahrenheit. Here are the typical temperature ranges for each material:
- Nitrile
- Low Temperature Usage: -30°F to -40°F | -34°C to -40 °C
- High Temperature Usage: Up to 250°F | 121°C
- Viton
- Low Temperature Usage: 10°F to -10°F | -12°C to -23°C
- High Temperature Usage: 400°F to 600°F | 204°C to 315°C
Cost
While Viton has the edge in a lot of areas, that specialty performance comes with a cost – quite literally. Simply put, Viton is a high-performance elastomer that will require a higher budget because it can perform in such demanding scenarios. Nitrile is also a specialty part, but it can be a much more cost-effective material if your performance requirements aren’t so demanding.
Nitrile vs. Viton: Invest in the Right Material for Your Parts
When you need tough materials that can handle oil and tough temperatures, Viton and Nitrile might be the perfect polymers for your parts. Of course, both rubbers are probably less suited for general purpose components. There are pros and cons to every compound, which is why it’s so critical to identify the best, most cost-effective solution for your parts.
Fortunately, Timco is here to help businesses invest in quality parts made for their exact needs. Ready to invest in quality parts custom-made for your application and budget? Give us a call at 800-969-6242 or contact us online about your part needs.